Sapevi che l’inventore dell’iPhone ha descritto in modo appropriato il miglioramento continuo?
Steve Jobs è una leggenda che ispira le aziende di tutto il mondo. Poco noto, ma vero: in una videointervista ha commentato il processo di miglioramento continuo (CIP). Secondo lui in molte aziende vale il motto “abbiamo sempre fatto così”. Questo è l’approccio tradizionale. Secondo Jobs, per pensare alla qualità contemporanea è necessario un principio diverso che si avvicina ai processi lavorativi in modo scientifico: “Allora c’è una teoria dietro il motivo per cui facciamo certe cose. C’è una descrizione di ciò che facciamo. E soprattutto c’è la possibilità di mettere sempre in discussione ciò che stiamo facendo”.
Jobs riconosce “una visione estremamente ottimistica delle persone che lavorano in azienda”. Il processo di miglioramento continuo (CIP) è la chiave per responsabilizzare i dipendenti: “Se hanno l’opportunità di cambiare e migliorare le cose, miglioreranno i processi se esiste un meccanismo per farlo. E trovo questo umanesimo ottimista molto attraente”. Questo meccanismo è il processo di miglioramento continuo (CIP). Prendiamo le parole ispiratrici di Steve Jobs come un’opportunità per dare uno sguardo più da vicino al CIP.
Lean productio spiegata in modo semplice
La guida introduce le misure più importanti per iniziare al meglio con la produzione snella. Scopri come ancorare il processo di miglioramento continuo (CIP) nella tua azienda.
GUIDA
Kaizen: filosofia dei piccoli passi e origine del CIP
Il processo di miglioramento continuo (CIP) è spesso equiparato a Kaizen, comportando molti malintesi. Kaizen è una filosofia di vita giapponese con una lunga tradizione: combina i termini giapponesi “Kai” (= cambiamento) e “Zen” (= in meglio), ossia cambiare in meglio. Questa tradizione di pensiero ha due presupposti fondamentali: da un lato, tutto nella vita può essere migliorato con piccoli passi; d’altra parte, questo miglioramento è infinito. Dietro questo c’è una visione positiva del mondo, ossia non devi accettare condizioni inadeguate, ma puoi migliorarle continuamente. Toyota riconobbe il potenziale di questa idea negli anni ’50, diventando la base del Toyota Production System (TPS). Ciò è stato associato a un errore positivo e a una cultura aziendale. La seguente citazione dell’inventore del TPS Taiichi Ohno lo riassume: “Non avere problemi è il problema più grande di tutti”. Questo la dice lunga sul CIP.
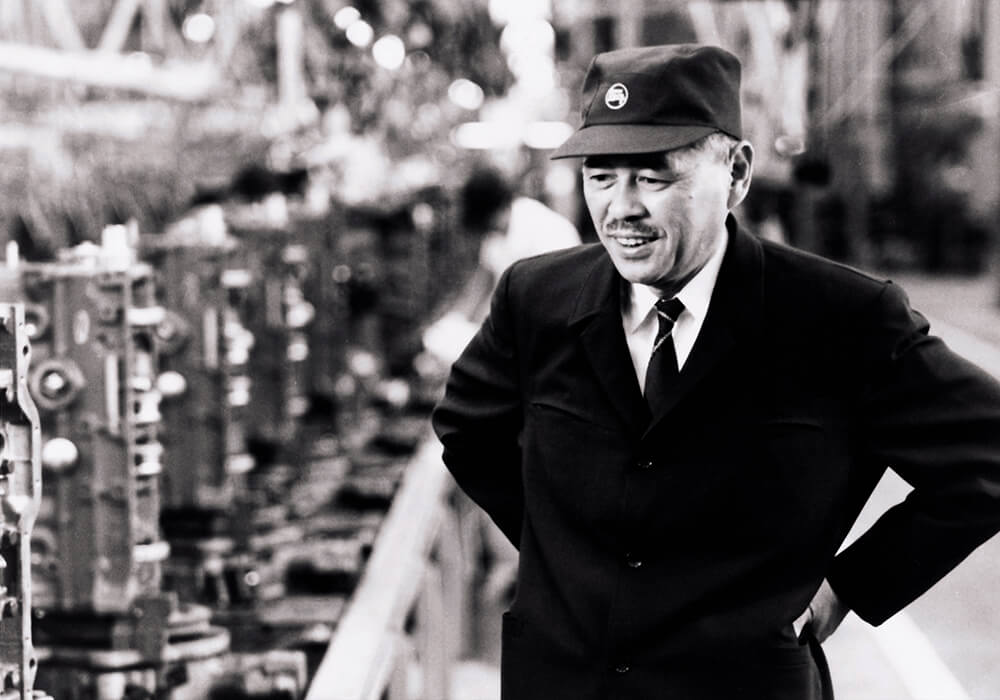
Storia e definizione di CIP
Nel 1990 è stato pubblicato il libro specialistico “The Machine That Changed the World: The Story of Lean Production”, introducendo i metodi della casa automobilistica giapponese Toyota alll’Occidente. L’abbreviazione “studio MIT” è più conosciuta, dove i tre autori descrivono il metodo di ottimizzazione del processo come un processo di miglioramento continuo (CIP). Toyota non usa questo termine. È così che puoi facilmente ricordare la differenza tra CIP e Kaizen: Kaizen va oltre il mondo del lavoro e prende in considerazione la vita nel suo insieme; attraverso il CIP, Kaizen continua a vivere oggi in Occidente come una sorta di filosofia Kaizen per le aziende. I metodi lean production non si trovano solo nell’industria, ad esempio anche nei contesti lean management o lean office. Il CIP è importante anche per la gestione della qualità secondo DIN EN ISO 9001. Qui ci limitiamo al CIP nella lean production e alle origini del metodo CIP. Steve Jobs per “umanesimo ottimista” intende lo sviluppo personale e la valorizzazione dei dipendenti.
Il miglioramento continuo significa rendere la produzione “più snella” con l’obiettivo di ridurre i tempi di lavorazione.
Il miglioramento continuo significa rendere la produzione “più snella” con l’obiettivo di ridurre i tempi di elaborazione. Una corsa va oltre la produzione. I tempi morti durante lo stoccaggio o tra i diversi processi sono parte integrante. La riduzione dei tempi di consegna ha un impatto positivo sulla produttività. Entrambi sono strettamente collegati. Il CIP porta direttamente al centro della produzione snella: “Lean production è la filosofia del miglioramento continuo”, afferma Thomas Hytzki, un esperto del lean che lavora in item da diversi anni. I tempi di produzione ridotti hanno molti effetti positivi: “L’alta qualità, i bassi costi e una buona flessibilità si ottengono solitamente in automatico”.
Ruolo dei dipendenti e delle risorse nel miglioramento continuo
I dipendenti si trovano direttamente presso la Gemba (“luogo effettivo”), dove avviene la creazione di valore. Questa idea è cruciale per il CIP. È qui che entra in gioco la formulazione di Steve Jobs della “visione estremamente ottimistica” dei dipendenti: la lean production li incoraggia a contribuire con le proprie competenze e conoscenze. Allo stesso tempo, hanno bisogno delle strutture giuste. Una cultura lean e CIP crea libertà e opportunità di sviluppo, creando le basi per miglioramenti rapidi, continui e flessibili. È meglio che i dipendenti abbiano la propria officina CIP. Immaginando una checklist con il processo, le strutture e una stanza separata per il CIP. Cosa mancherebbe ancora in azienda? Esattamente i componenti giusti per processi snelli.
Adattare le risorse a nuovi requisiti e processi in qualsiasi momento. L’alluminio utilizzato è notevolmente più leggero dell’acciaio e le strutture rimangono definitivamente stabili.
Il sistema lean production è stato sviluppato direttamente per i requisiti della produzione snella. Coi suoi componenti si ha la base perfetta per la costruzione della attrezzature, la realizzazione di soluzioni come scaffali e carrelli di trasporto in modo rapido e semplice. I tubolari profilati D30 sono al centro del sistema lean. È possibile effettuare tutte le connessioni a 90 gradi da solo con una persona, uno strumento e un tipo di connettore, risparmiando sui costi di assemblaggio e stoccaggio. Il sistema modulare e la tecnica di collegamento intuitiva semplificano notevolmente l’implementazione. Le connessioni possono essere facilmente rimosse. Si ha quindi la flessibilità necessaria per il CIP: adattando in qualsiasi momento le risorse alle nuove esigenze e ai nuovi processi, migliorano continuamente la fornitura di materiali e i processi di produzione. L’alluminio utilizzato è notevolmente più leggero dell’acciaio e le strutture rimangono permanentemente stabili. Qui sono disponibili alcune soluzioni esplicative.
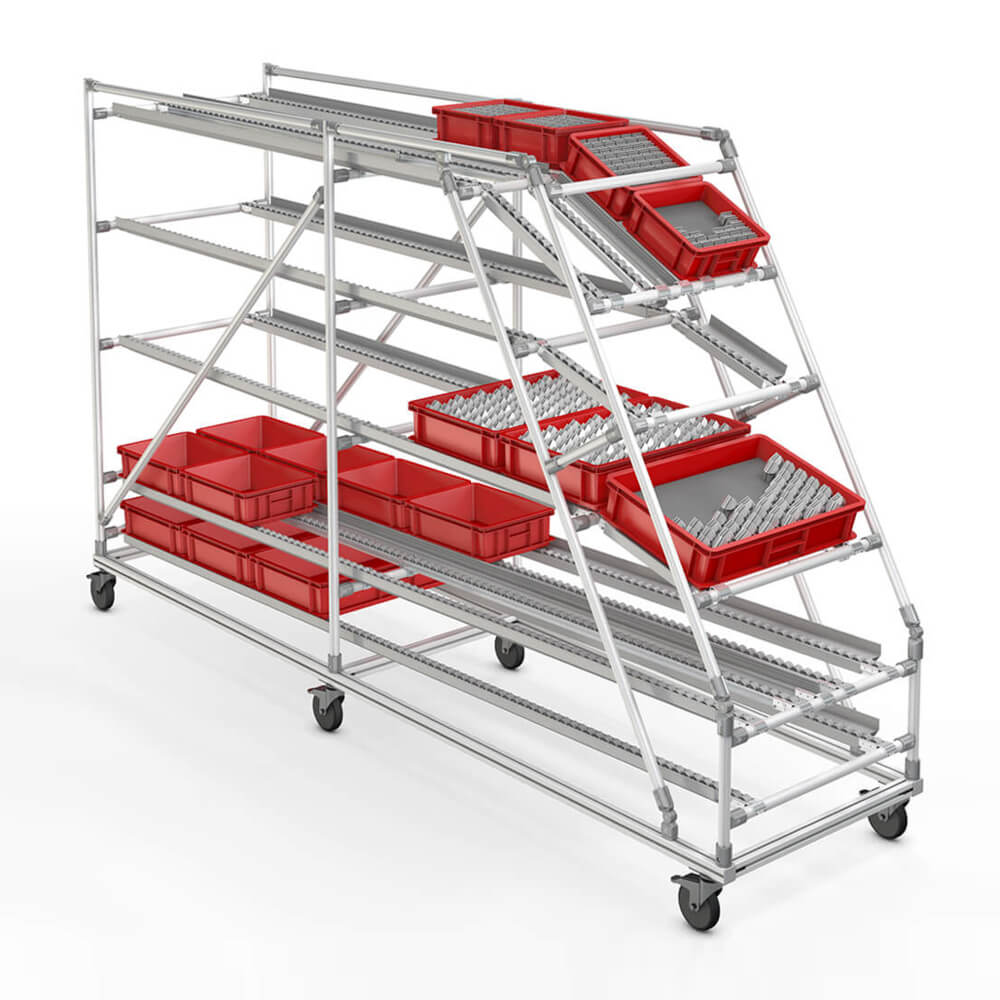
3M: le sfide per il miglioramento continuo
Il CIP non si concentra sugli errori gravi; si tratta invece di piccoli dettagli in cui i miglioramenti, alla fine, fanno una grande differenza. La riduzione dei tempi di produzione è alla base del CIP. Ci sono tre principali cause di tempi di produzione elevati: muda (spreco), mura (squilibrio) e muri (sovraccarico), definiti “3M” per la prima lettera in comune:
- Muda: si riferisce ad un’attività che non contribuisce alla creazione di valore. Dal punto di vista della lean production, si tratta di “spreco” ed è inutile. Sono conosciute complessivamente 7 tipologie di spreco (= 7 Muda). Lo spettro spazia dai movimenti di materiale non necessari, agli scarti e alle rilavorazioni. Esistono contromisure efficaci per tutti i Muda.
- Mura: si verifica uno squilibrio quando le risorse non vengono utilizzate equamente. Una postazione di lavoro è sottoposta ad un utilizzo eccessivo, l’altra a uno stress minimo o nullo. Davanti alla stazione sovraffollata si formano code, aumentando i tempi di lavorazione. Allo stesso tempo, la stazione poco utilizzata crea poco valore aggiunto.
- Muri: un carico eccessivo di una stazione può portare a un sovraccarico: questo vale sia per i dipendenti che per il materiale. La pressione del tempo porta rapidamente a stress fisico e psicologico per i dipendenti. Le macchine corrono il rischio di usurarsi, soprattutto perché la qualità del prodotto può risentirne.
Muda è più spesso al centro dell’attenzione rispetto a Mura e Muri. Non c’è da stupirsi, perché il concetto è particolarmente chiaro. La vera fonte di spreco non è Muda, bensì Mura. I processi sbilanciati portano a ulteriori conseguenze negative. Quindi le aziende non dovrebbero concentrarsi solo su Muda.
Implementazione del processo di miglioramento continuo (CIP) col ciclo PDCA
Come si può concretamente avviare il CIP? Uno degli esempi più chiari di CIP è il ciclo PDCA. Ciò fornisce un metodo pratico per l’attuazione del CIP. Bisogna considerare che la lean production si basa sull’interazione di diversi metodi. Gli obiettivi vengono definiti utilizzando la mappatura del flusso di valore e il progetto del flusso di valore. Solo allora entra in gioco il ciclo PDCA, il quale deve il proprio nome alla prima lettera dei suoi quattro passaggi: “Plan”, “Do”, “Check” e “Act”. Bisogna definire solo una misura per ciclo PDCA, mentre il processo e i passaggi sono sempre gli stessi con PDCA:
Plan:
Osservare i processi e lo stato attuale in loco. È fondamentale rivolgersi direttamente ai dipendenti, identificare i processi che necessitano di miglioramento e sviluppare un piano per iniziare il miglioramento continuo. Raccogliendo numeri, dati e fatti, sia ha la base per definire le misure per raggiungere lo stato dell’obiettivo.
Do:
Il PDCA consiste nel provare cose su piccola scala, implementando un’idea in un esperimento pratico. Viene testata una sola misura: così è possibile facilmente capire causa ed effetto. Se qualcosa non funziona, non ha molto impatto. Questo è il vantaggio di esperimenti così piccoli.
Check:
Ora è il turno della valutazione, analizzando tutte le misure adottate: cosa ha avuto o meno successo? quali sono state le ragioni del successo o del fallimento? è concepibile una strategia concreta per tutta l’azienda? Solo allora si dovrebbe guardare al quadro generale.
Act:
Ora è possibile intraprendere un’azione più grande, documentarla e rivederla. Sono possibili anche workshop o l’acquisto di nuove attrezzature. Le misure hanno avuto successo? Standardizzandole, il processo PDCA ricomincerà.
Il PDCA mostra chiaramente cosa costituisce il CIP. È possibile collegare le parole di Steve Jobs alla natura scientifica del metodo. Esiste una teoria per le misure, che vengono descritte e messe in discussione in dettaglio. Ecco come si chiude il cerchio in ambito CIP: