Czy wiesz, że wynalazca iPhone’a bardzo trafnie opisał proces ciągłego doskonalenia?
Steve Jobs to prawdziwa legenda, która inspiruje przedsiębiorstwa na całym świecie. Niewielu o tym wie, ale prawdą jest, że: Steve Jobs w jednym z wideo-wywiadów odniósł się do procesu ciągłego doskonalenia. Jego zdaniem w wielu firmach obowiązuje zasada „przecież zawsze tak to robiliśmy”. To jest klasyczne podejście. Aby w zarządzaniu jakością iść jednak z duchem czasu, koniecznie jest wdrożenie innych zasad. Nowe koncepcje rozpatrują procesy robocze naukowo: „Wówczas za przyczyną robienia przez nas określonych rzeczy, stoi odpowiednia teoria. Istnieje opis tego, co robimy. Ale przede wszystkim zawsze istnieje możliwość, aby to, co robimy, sprawdzić.”
Jobs dostrzegł w tym podejściu „wyjątkowo optymistyczne spojrzenie na ludzi, którzy pracują w firmie”. Proces ciągłego doskonalenia (ang. Continual Improvement Process, CIP) to klucz do tego, aby umożliwić pracownikom rozwój: „Jeśli pracownicy będą mieli możliwość zmiany określonych rzeczy i ich ulepszenie, będą udoskonalać procesy, pod warunkiem, że będzie istniał do tego odpowiedni mechanizm. I takie optymistyczne, humanistyczne podejście bardzo do mnie przemawia.” Tym mechanizmem jest proces ciągłego doskonalenia (CIP). Niech inspirujące słowa Steve’a Jobsa będą okazją, aby przyjrzeć się temu procesowi bliżej.
Produkcja Lean w kilku łatwych słowach
Idealny sposób na szybkie wdrożenie koncepcji szczupłej produkcji: W bezpłatnym przewodniku dowiesz się, jakie środki i działania mają naprawdę znaczenie. Poznasz również sposób na wdrożenie procesu ciągłego doskonalenia we własnym przedsiębiorstwie.
POBIERZ TERAZ
Kaizen: filozofia małych kroków i początek CIP
Proces ciągłego doskonalenie często mylony jest z koncepcją Kaizen, co prowadzi do nieporozumień. Kaizen to japońska filozofia życia, która ma bardzo długą historię. Słowo Kaizen składa się z dwóch wyrazów: „Kai” (= zmiana) i „Zen” (= ku lepszemu). Widać tutaj istotę tej koncepcji: zmiany na lepsze. To filozoficzne podejście opiera się na dwóch podstawowych założeniach. Po pierwsze, wszystko w życiu można ulepszyć małymi krokami. Po drugie, zmiany nie mają końca. Kryje się za tym pozytywne spojrzenie na świat: nie ma potrzeby godzenia się na rzeczy, które nie są zadowalające, ponieważ zawsze można je ulepszyć. Potencjał tego podejścia odkryli w Toyocie już w latach 50-tych XX wieku. Stało się ono fundamentem systemu produkcyjnego Toyoty (Toyota Production System, TPS), z którym łączy się pozytywna idea konstruktywnej nauki na błędach i kultury przedsiębiorstwa. Taiichi Ohno, ojciec TPS, tak mówił o istocie swojej koncepcji: „Brak problemów to największy problem ze wszystkich.” To bardzo wiele mówi o procesie ciągłego doskonalenia.
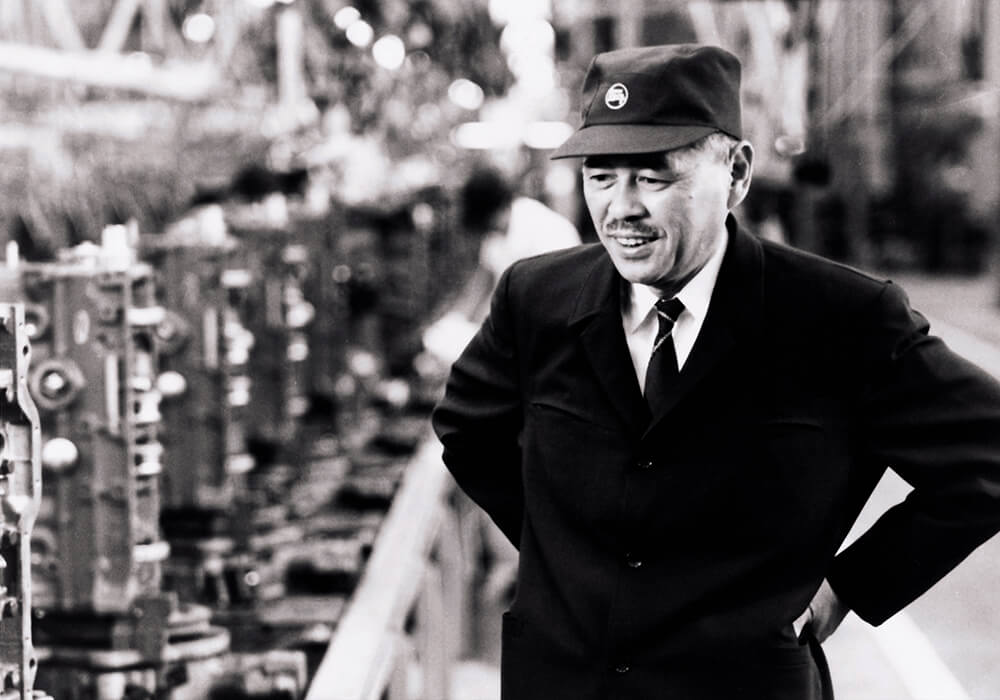
Historia i definicja procesu ciągłego doskonalenia
W 1990 roku pojawiła się na rynku książka „The Machine That Changed the World: The Story of Lean Production“, która zaprezentowała Zachodowi metody stosowane w Toyocie, japońskim koncernie samochodowym. Bardziej popularny jest skrót „badania na uniwersytecie MIT”. W książce jej trzej autorzy opisują metodę optymalizacji procesu jako proces ciągłego doskonalenia (CIP). W Toyocie nie używano tego pojęcia. Łatwo zapamiętać sobie różnicę między CIP a Kaizen: Kaizen wykracza poza świat zawodowy i dotyczy całego życia. Filozofia Kaizen dzisiaj realizowana jest na Zachodzie w postaci procesu ciągłego doskonalenia i stanowi koncepcję Kaizen dla przedsiębiorstw. Metody produkcji Lean wdrażane są nie tylko w zakładach przemysłowych. Wystarczy wspomnieć tutaj chociażby o zarządzaniu Lean lub Lean Office. Proces ciągłego doskonalenia stał się również ważnym założeniem systemu zarządzania jakością według normy DIN EN ISO 9001. W tym miejscu ograniczymy się jedynie do procesu ciągłego doskonalenia w produkcji Lean. Ważne jest, aby uzmysłowić sobie korzenie metody CIP. Mówiąc o „pozytywnym, humanistycznym podejściu”, Steve Jobs miał na myśli: Osobisty rozwój pracowników i szacunek dla nich.
Proces ciągłego doskonalenia polega na tym, aby „odchudzić” produkcję. Celem jest skrócenie czasu trwania cyklu operacyjnego.
Proces ciągłego doskonalenia polega na tym, aby „odchudzić” produkcję. Celem udoskonaleń jest skrócenie czasu trwania cyklu operacyjnego. Cykl operacyjny wykracza poza ramy procesu produkcyjnego. Jego stałą częścią jest czas oczekiwania, np. w wyniku magazynowania lub pomiędzy różnymi procesami. Skrócenie czasu trwania cykli operacyjnych ma pozytywny wpływ na wydajność. Oba te czynniki są ściśle ze sobą powiązane. Proces ciągłego doskonalenia prowadzi nas do samego centrum szczupłej produkcji: „Produkcja Lean to koncepcja ciągłego udoskonalania”, wyjaśnia Thomas Hytzki, specjalista ds. Lean i wieloletni pracownik item. Skrócony czas trwania cykli operacyjnych ma wiele pozytywnych skutków: „Wysoka jakość, niskie koszty oraz elastyczność pojawiają się zwykle automatycznie.”
Rola pracowników oraz środków produkcji w procesie ciągłego doskonalenia
Pracownicy znajdują się bezpośrednio w miejscu zdarzenia – Gemba (= „miejsce wykonywania rzeczywistej pracy“). To tutaj tworzone są wartości. To założenie ma w procesie ciągłego doskonalenia decydujące znaczenie. Wróćmy teraz do sformułowania użytego przez Steve’a Jobsa dotyczącego pracowników i „wyjątkowo optymistycznego spojrzenia” na nich: produkcja Lean zachęca ich, aby podzielili się swoim doświadczeniem i swoją wiedzą. Do tego potrzebne są odpowiednie struktury. Kultura oparta na zasadach Lean i procesie ciągłego doskonalenia zapewnia przestrzeń i szanse na rozwój. W ten sposób powstaje fundament pod szybkie, ciągłe i elastyczne ulepszenia. Idealnie jest, jeśli pracownicy mają do dyspozycji własny warsztat CIP. Wyobraź sobie krótką checklistę: proces, struktury i własne pomieszczenie do realizacji procesu ciągłego doskonalenia. Czego w przedsiębiorstwie jeszcze brakuje? Zgadza się: odpowiednich komponentów potrzebnych do szczupłych procesów.
Dopasowuj środki produkcji do nowych wymagań i procesów zgodnie z potrzebami. Zastosowane aluminium jest znacznie lżejsze od stali. Wykonane z niego konstrukcje wyróżniają się również trwałą stabilnością.
Nasz system modułowy Lean Production został opracowany specjalnie dla wymogów szczupłej produkcji. Elementy wchodzące w skład tego systemu to idealny fundament pod budowę środków produkcji. Przy ich użyciu możesz szybko i łatwo wykonać takie rozwiązania jak regały i wózki transportowe. System profili rurowych D30 to serce naszego systemu Lean. Wszystkie połączenia pod kątem 90 stopni możesz wykonać samodzielnie. Do ich budowy wystarczy jedna osoba, jedno narzędzie i jeden rodzaj łącznika. W ten sposób zaoszczędzisz na kosztach montażu i magazynowania. Budowę nowych konstrukcji dodatkowo ułatwiają modułowy system oraz intuicyjna technika łączenia. Już gotowe połączenia można bez trudu rozłączyć. Z tym systemem masz zapewnioną elastyczność, która przyda się w procesie ciągłego doskonalenia. Dopasowuj środki produkcji do nowych wymagań i procesów zgodnie z potrzebami. W ten sposób zadbasz o ciągłe doskonalenie systemów służących do dostarczania materiałów i procesów wytwórczych. Zastosowane aluminium jest znacznie lżejsze od stali. Wykonane z niego konstrukcje wyróżniają się również trwałą stabilnością. Chcesz zobaczyć przykładowe rozwiązania? W takim razie skorzystaj z dostępnych tutaj rozwiązań wzorcowych i zainspiruj się.
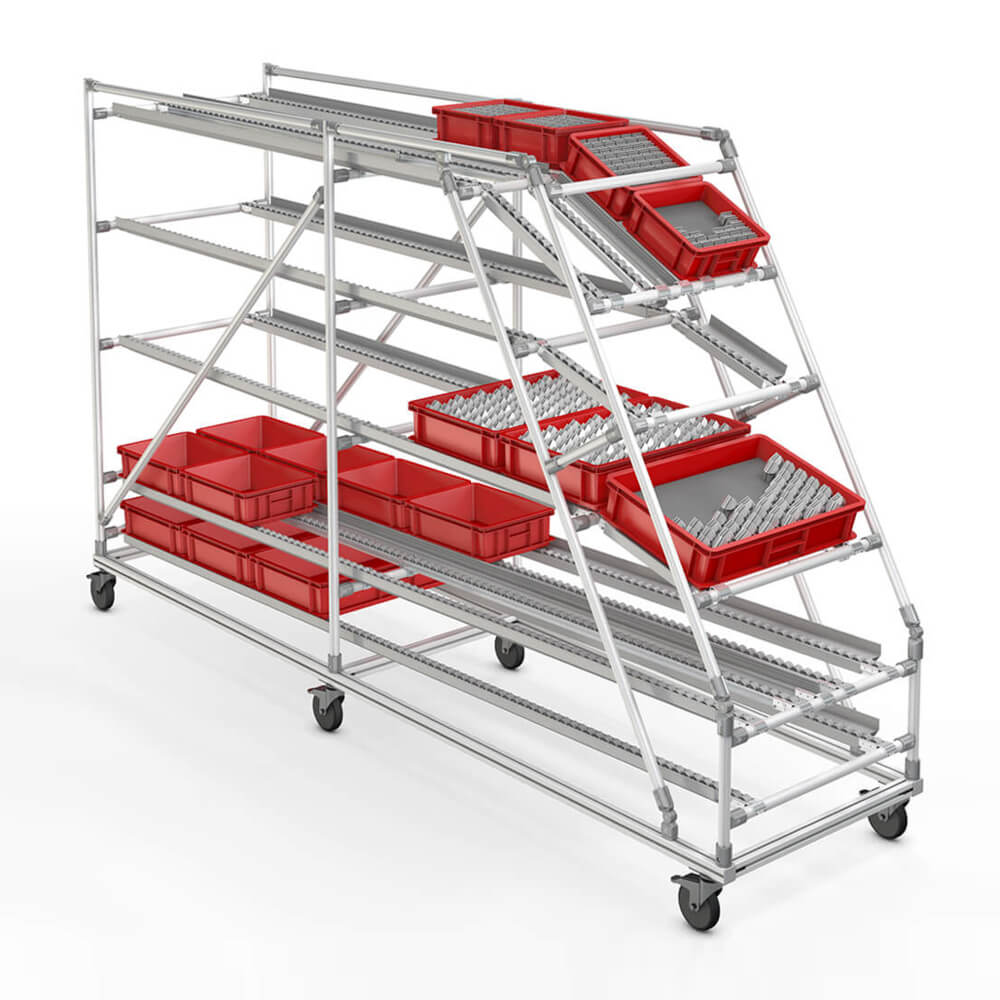
3M: wyzwania związane z ciągłym doskonaleniem
Proces ciągłego doskonalenia nie skupia się na poważnych błędach, lecz na małych szczegółach, które po ulepszeniu zapewniają wielki efekt. Najważniejszym celem procesu ciągłego doskonalenia jest skrócenie czasu trwania cyklu operacyjnego. Za długie cykle operacyjne odpowiadają przede wszystkim następujące trzy przyczyny: muda (strata), mura (zmienność) i muri (przeciążenie). Ze względu na literę, na jaką zaczynają się te czynniki, nazywane są również „3M”:
- Muda: jest to czynność, która nie przyczynia się do tworzenia wartości. Z perspektywy produkcji Lean „strata” nie ma żadnego uzasadnienia. Łącznie znanych jest 7 rodzajów strat (= 7 muda), które obejmują m.in. niepotrzebny transport, wybrakowane wyroby oraz konieczne poprawki. Każdy rodzaj muda ma odpowiedni dla siebie środek zapobiegawczy.
- Mura: jeśli zasoby nie są wykorzystywane równomiernie, dochodzi do zaburzenia równowagi. Jedna stacja robocza jest za bardzo obciążona, tymczasem inna wykorzystywana jest jedynie w nieznacznym stopniu lub wcale. Przed stacją, która jest obciążona za mocno, tworzą się kolejki. Takie zjawisko wpływa na wydłużenie cykli operacyjnych. Jednocześnie na stacji, która jest obciążona w niedostatecznym stopniu, nie tworzy się wartości lub tworzy się jej za mało.
- Muri: nadmiernie obciążona stacja robocza skutkuje przeciążeniem, które dotyczy zarówno pracowników, jak i materiałów. Presja czasu szybko powoduje u personelu psychiczne i fizyczne obciążenie. Istnieje zagrożenie nadmiernego zużycia się maszyn, co może prowadzić do pogorszenia się jakości wyrobów.
Muda to rodzaj marnotrawstwa, które jest częściej w centrum uwagi niż Mura czy Muri. To nic dziwnego, w końcu ta koncepcja jest bardzo obrazowa. Jednak prawdziwym źródłem strat nie jest Muda a Mura. Z niewyważonymi procesami związane są jeszcze inne negatywne skutki. Dlatego przedsiębiorstwa powinny swoją uwagę skupiać nie tylko na Muda.
Realizacja procesu ciągłego doskonalenia (CIP) na podstawie cyklu PDCA
W jaki sposób rozpocząć proces ciągłego doskonalenia? Do najbardziej obrazowych przykładów procesu ciągłego doskonalenia należy cykl PDCA. To bardzo praktyczna i przydatna metoda w jego realizacji. Ważne: Produkcja Lean opiera się na łączeniu ze sobą różnych metod. Na początku określa się cele za pomocą takich technik jak mapowanie i projektowanie strumienia wartości. Dopiero później realizowany jest cykl PDCA. Jego nazwa pochodzi od pierwszych liter czterech etapów, z których się składa. „Plan“, „Do“, „Check“ i „Act“. W ramach jednego cyklu PDCA należy określić tylko jedno działanie. Przebieg cyklu oraz jego etapy zawsze są takie same:
Plan:
Obserwuj procesy i stan aktualny bezpośrednio na miejscu. Decydujące znaczenie ma bezpośredni kontakt z pracownikami. Zidentyfikuj procesy wymagające poprawy i opracuj plan działania. To on ma uruchomić proces ciągłego doskonalenia. Gromadź dane liczbowe, informacje i fakty. To jest podstawa do ustalenia działania służącego do osiągnięcia stanu docelowego.
Do:
W cyklu PDCA chodzi o to, aby nowe pomysły wprowadzać w życie na małą skalę. Pomysły realizuj w praktyce. Wykonuj jednocześnie tylko jedno działanie: dzięki temu możesz bez trudu ustalić przyczyny i skutki. Jeśli coś nie zadziała, nie ma to większego wpływu na całość. To jest właśnie zaleta eksperymentów przeprowadzanych w małym wymiarze.
Check:
Teraz czas na analizę. Zastanów się nad wszystkimi przeprowadzonymi działaniami. Które z nich były skuteczne, a które nie? Co byłą przyczyną sukcesów i porażek? Czy istnieje możliwość wdrożenia określonej strategii w całym przedsiębiorstwie? Dopiero po uzyskaniu odpowiedzi na te pytania należy przyjrzeć się całemu problemowi.
Act:
Teraz czas na wdrożenie szerzej zakrojonych działań. Prowadź ich dokumentację i sprawdzaj je. Dobrym rozwiązaniem są również warsztaty oraz zakup nowego wyposażenia. Czy przeprowadzone przez Ciebie działania były skuteczne? W takim razie poddaj je standaryzacji. W przeciwnym razie cykl PDCA należy rozpocząć jeszcze raz.
Cykl PDCA bardzo obrazowo pokazuje, na czym polega proces ciągłego doskonalenia. Słowa Steve’a Jobsa o naukowym podejściu do procesu ciągłego doskonalenia można odnieść bezpośrednio do tej metody. Istnieje teoria dotycząca działań, które zostały szczegółowo opisane i sprawdzone. Na koniec oddajmy mu głos: W myśl procesu ciągłego doskonalenia tutaj zamyka się obieg.
Interesują Cię ciekawe historyjki i nowości świata produkcji lean? W takim razie mamy coś dla Ciebie: Zapisz się do blogowego newslettera item, wykorzystując do tego baner w prawym górnym rogu!